Polyblok Pools
I. Polybloks
The Bluepools Polybloks are ICF (Insulated Concrete Forms) that are very light and fit together like Legobricks. They form a hollow wall that is filled with concrete and reinforcement which forms an insulated wall of very high strength reinforced concrete that is indestructible.
Furthermore, the foam used in ICFs will not burn. It will melt if exposed to high heat, but it will not contribute any fuel to the fire. In fact, it is virtually “self-extinguishing,” thanks to a flame retardant all the leading ICF manufacturers add to the EPS foam.
More Polyblok Images
II. Construction with Polybloks
Polyblok Pool Construction
The combination of Polyblok pool walls, waterproofed with a premium quality vinyl liner that will last for 20 years simply provides the best swimming pools currently available at a very economic cost.
Vinyl liners last far longer than the joints in tiled pools, look just as attractive as a tiled pool, provide a far greater variety of colours and textures and cost about 20-30% of the price.
The Polybloks are also very light and easy to handle and the pool walls can be built in a few days when the concrete is pumped into them from the road using a concrete pump that will cost about £500 for the hire.
Every other type of pool tank provides very poor value for money when compared with a Polyblok pool that has been waterproofed with a vinyl liner.
Vinyl Liners
Better Than Fibreglass Pools
Factory made fibreglass pools are the cheapest pool type offered by most UK pool installers. The better quality fibreglass pools made under the strict control of a factory environment can last up to 10 years before the gel coat starts to fail, but the shiny pool surface will start to loose its sheen long before then.
Every fibreglass pool will eventually need to be either renewed or disposed of because the very attractive shiny gel coat that it arrives with can only be produced under strictly controlled factory conditions and cannot be repaired or renewed on site. And the excavation and disposal of the fibreglass shell and surrounding concrete ring beam will be nearly as expensive as a brand new pool and can adversely effect the value of the property in which it is built.
Another primary disadvantage of fibreglass pools is that the deck level versions are only made on a bespoke basis. Most top quality pools are now built with deck level pool technology that provides far superior water quality and a stunning appearance that simply cannot be matched by a freeboard fibreglass pool with its intrusive perimeter beam stiffening system that cannot be totally hidden by coping stones.
Deck Level Pool
Polyblok Pool Halls
Bluepools is a strong advocate of the construction of pool halls up to eaves level in the same Polybloks that it uses for the pool walls. There are two fundamentally important reasons for this:
1. Reduce Overall Construction Time & Costs
The reinforced Polyblok walls have enough strength to resist wind loading and as a result, steel or glulam (laminated timber) frames are not required. The frames are very costly, specially manufactured items and they increase the width of the pool hall by about 500mm causing a further increase in cost. The Polyblok walls may be more expensive than conventional block cavity walls but will still save money on overall cost and can reduce the construction time by a several months.
2. Reduce Running Costs
Tests have proven that all ICF (Insulated Concrete Forms) built houses are far more draught proof than any other form of construction. The Polybloks that Bluepools uses have another unique advantage that arises as a result of the stainless steel wire inserts that hold the leaves together during concreting. It has been shown that the stainless steel inserts spread the interior heat into the concrete core of the Polyblok. As a result the temperature gradient between the pool hall and the core of the concrete wall is very low, leading to much less heat loss from the pool hall air. As a result, pool halls built in Polybloks will cost far less to operate than a pool hall built with conventional cavity walls with cavity batts or any form of timber construction that is notorious for incorporating gaps where the heat is carried away by draughts.
Pool Hall Construction
III. Benefits provided by Polybloks
Bluepools uses a special Polyblok that is manufactured in the UK and has many intrinsic advantages including:
- They have an Agréement Certificate which means all Building Control Officers will accept them - and more importantly every UK building insurance company will provide cover for a building utilising them.
- They can be used to build basement and pool hall walls as well as the actual pool (of any shape/depth)
Pool Halls
- They can be tiled or fitted with a vinyl liner and will provide the cheapest method of tiled pool construction
Tiles or Vinyl Liners
- They are 1200 x 600mm and can be 280mm or 330mm wide allowing the construction of 150mm or 200mm reinforced concrete walls.
- They provide 130mm of dense polystyrene insulation - more than is required by the Building Regulations.
- They have stainless steel inserts that allow finishes to be fixed to either side of the wall with self tapping screws.
- They have high structural strength that will resist ice loading and even earthquakes because the concrete wall formed inside the Polybloks is much stronger than a wall formed with wooden shutters because the concrete cures (dries out and strengthens) much more slowly inside the polystyrene leaves.
- They are easily the fastest and cheapest way to build pool tanks and retaining walls because expensive specialists and equipment are not required on the site!
Pool Tanks
- They facilitate the fitting of the Through the wall equipment because submerged lights and skimmers are easily installed by cutting into the polystyrene leaves. The equipment is then fixed in place with tie wires or cable tiles to the rebar or stainless steel ICF wires.
IV. The Bluepools Polybloks
The images below illustrate just how flexible the Polybloks are when a small but very complex pool hall is being built - just click on the images for larger versions:
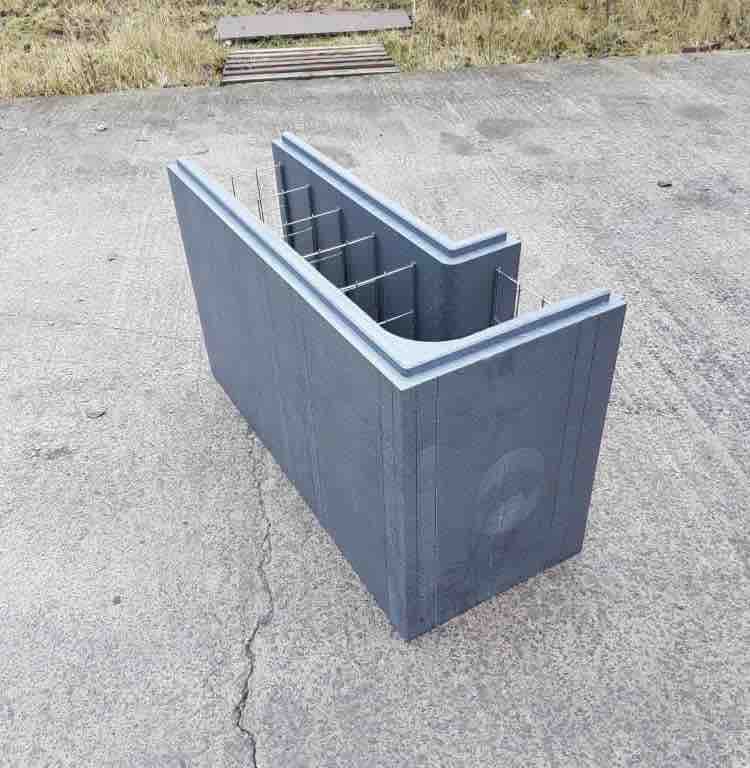 |
These polybloks are used in the corners.
(980mm x 380mm x 280mm) |
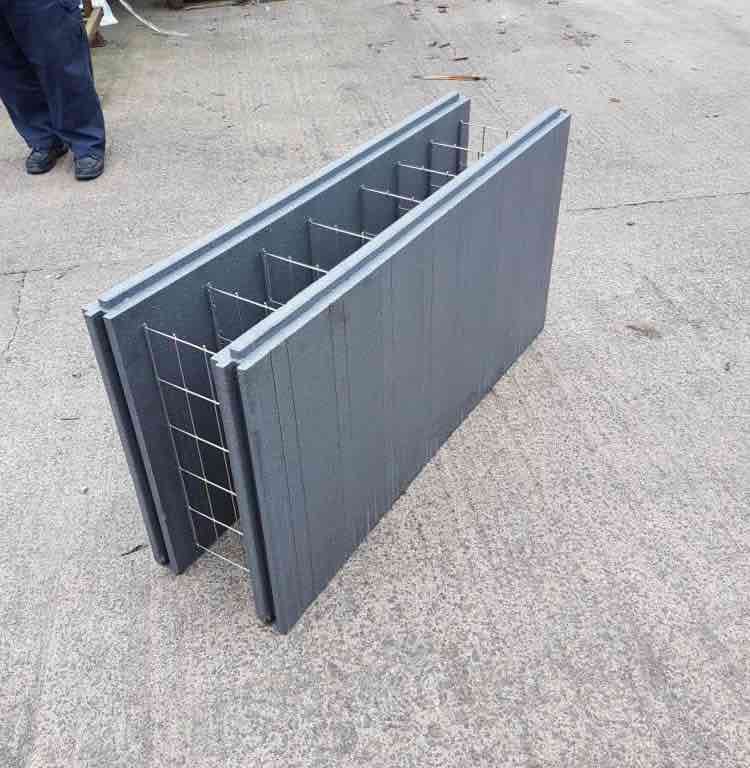 |
These are the straight blocks.
(1200mm x 600mm x 280mm)
The stainless steel wires connect the stainless steel plates that lie about 10mm below the surface of the polystyrene and are about 30mm wide. These parts hold the leaves together when the wet concrete exerts high lateral pressures after the form has been filled. |
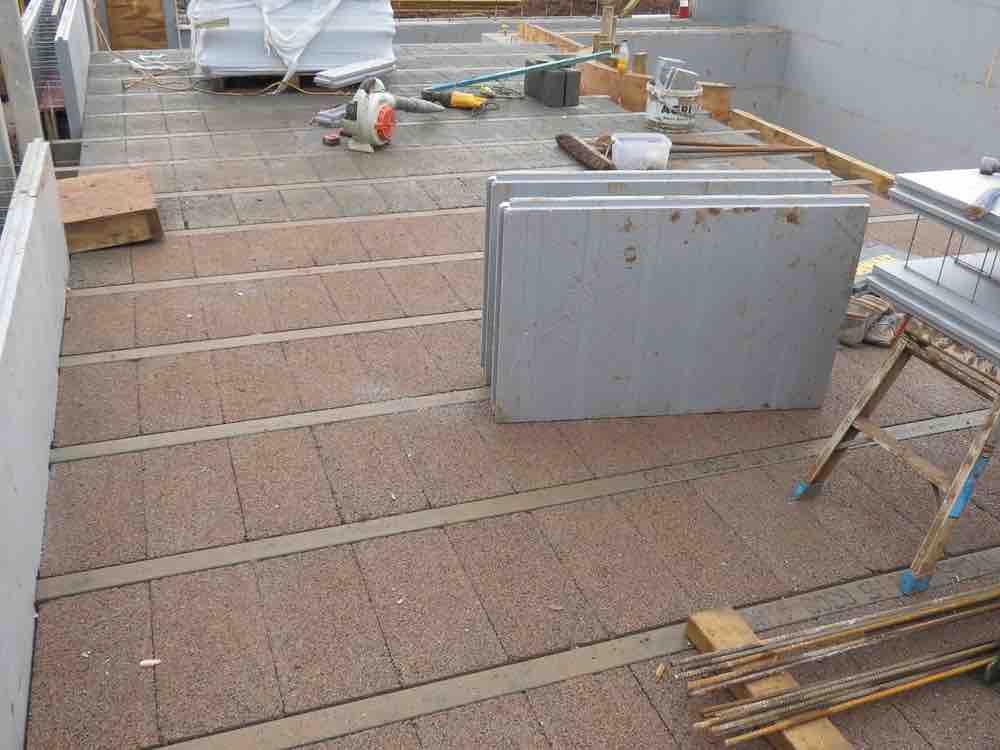 |
Here is an indoor commerical (hotel) pool being built with Polybloks.
Note how easily the beam and block floor can be installed by filling the polybloks up to the underside of floor level. |
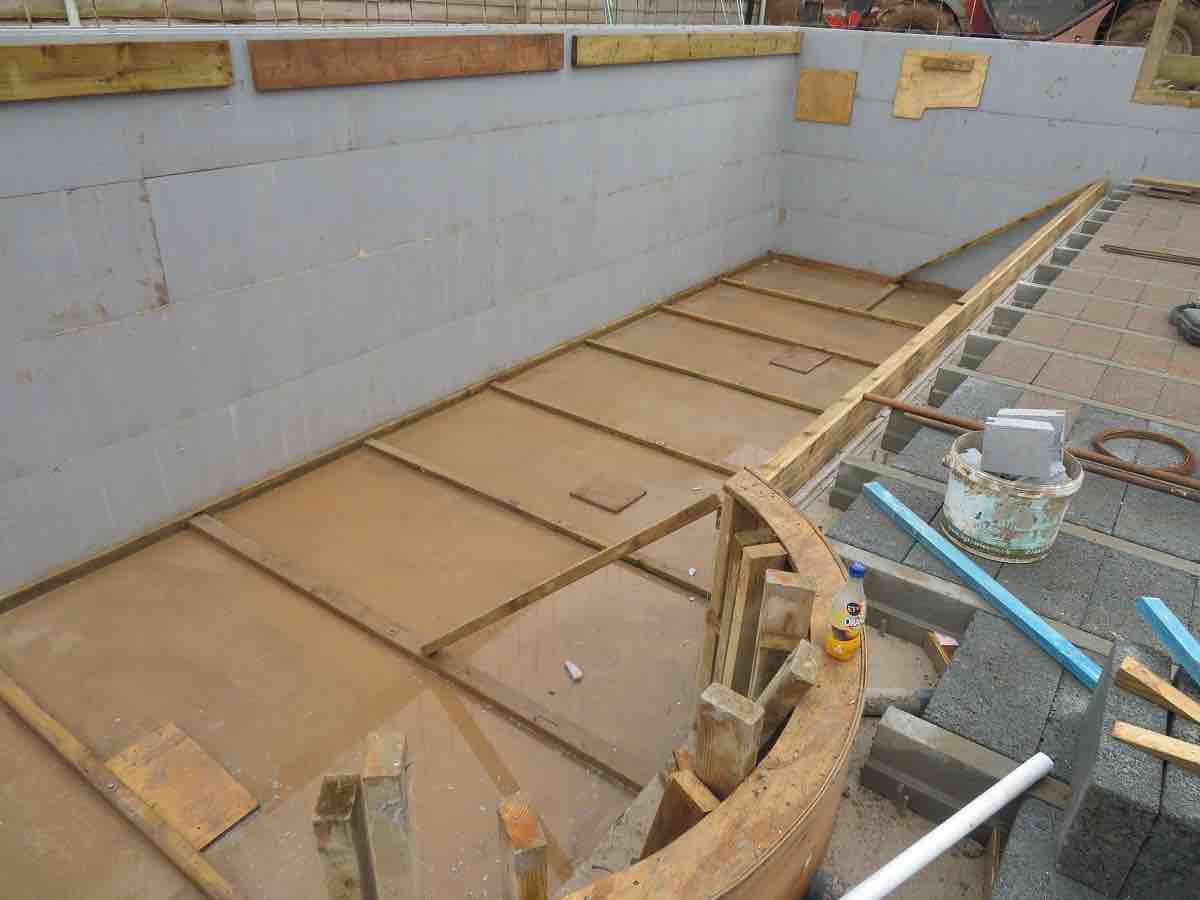 |
Here you can see the pool area with semicircular steps in the foreground.
The timbers on the floor are to restrain the polybloks in position when being filled with concrete. |
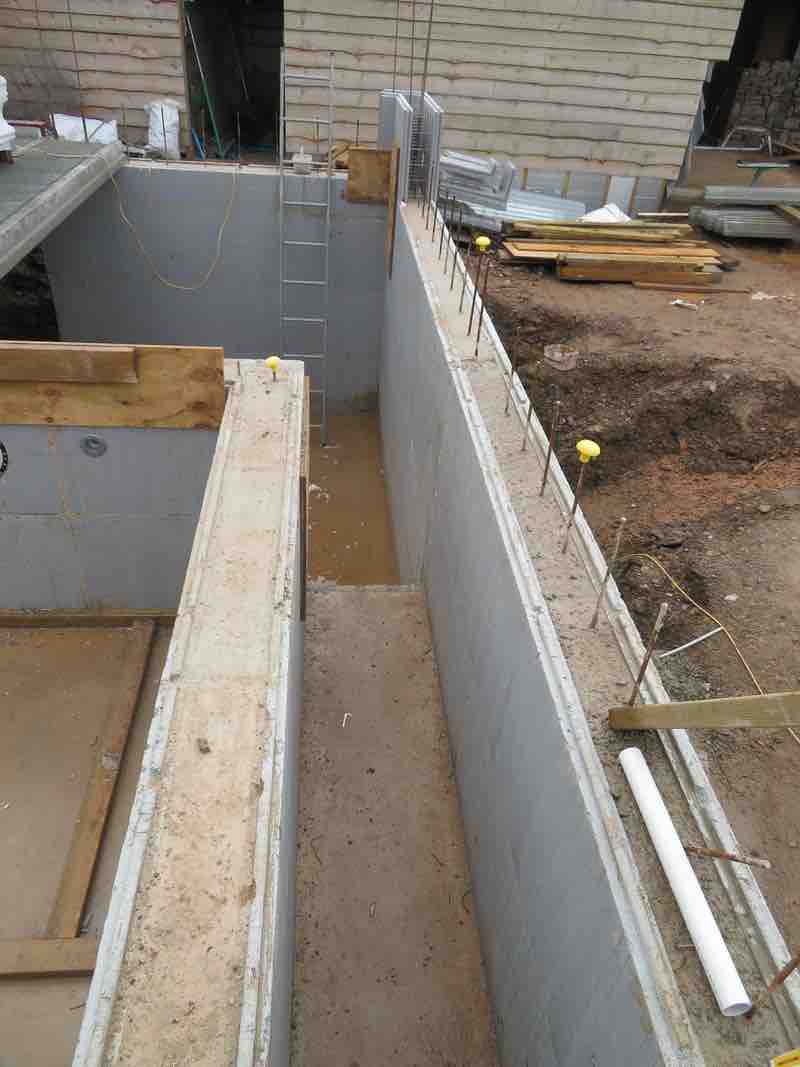 |
The pool wall on the left will need to be raised with coping stones as it will become the infinity edge. This will be higher than the window cill that is to be positioned on the right, where a large window overlooking the scenery will be installed.
The area at the top will hold a 6 person bespoke hydro-spa. |
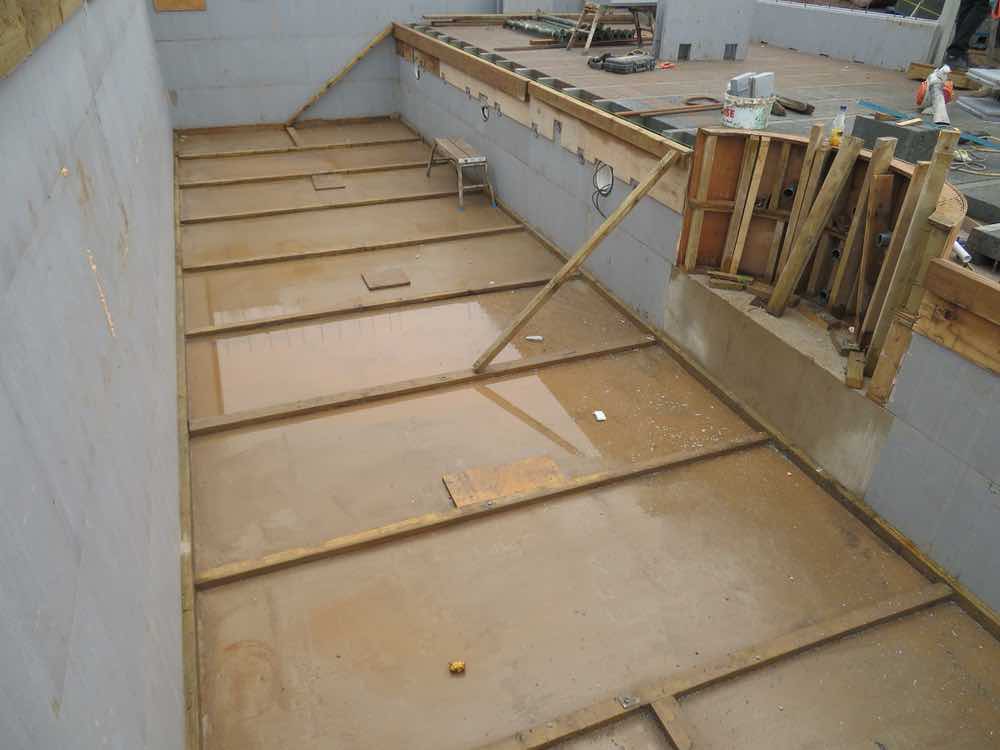 |
Note the 63mm pipes through the step. These are for Submerged LED colour lights. |
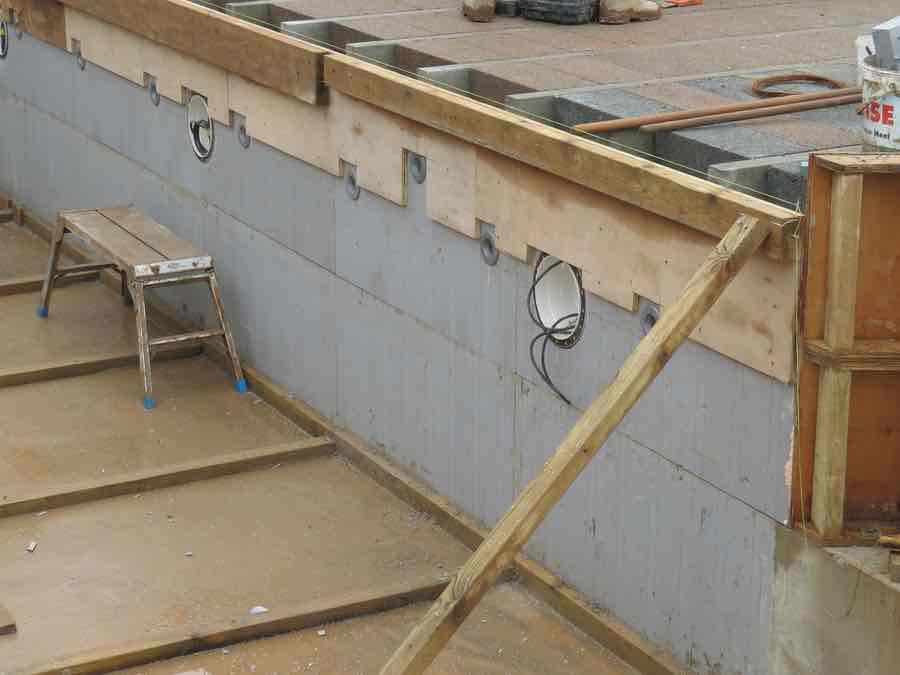 |
"Through the wall pool equipment fittings".
Note the large diameter submerged LED lights and the numerous water inlets that comply with the Bluepools "Clear Clean Water" principles. |
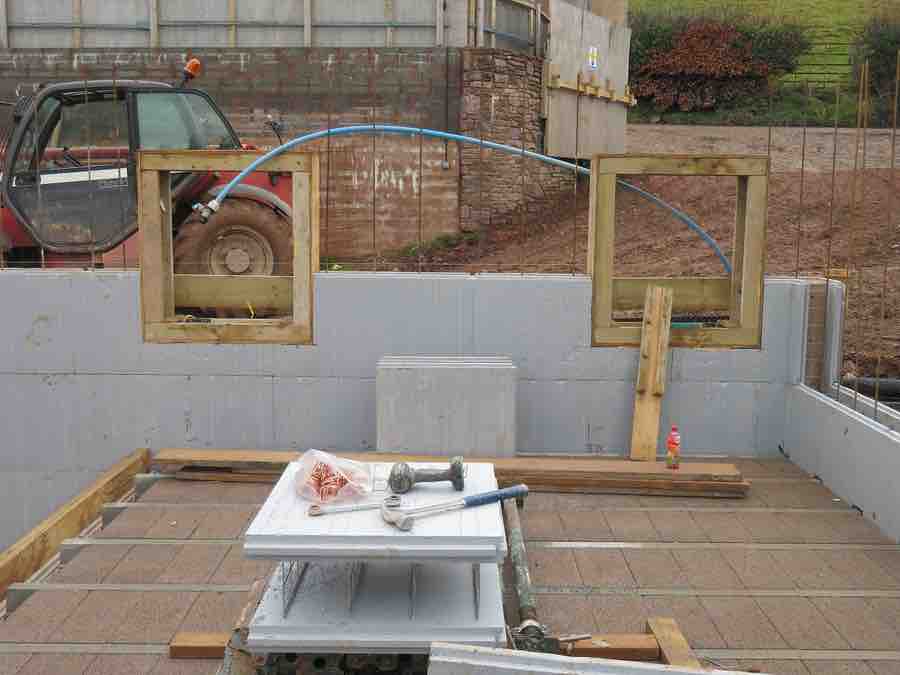 |
This image illustrates how easy it is to form voids in the Polyblok walls. In this case the voids are for windows. |
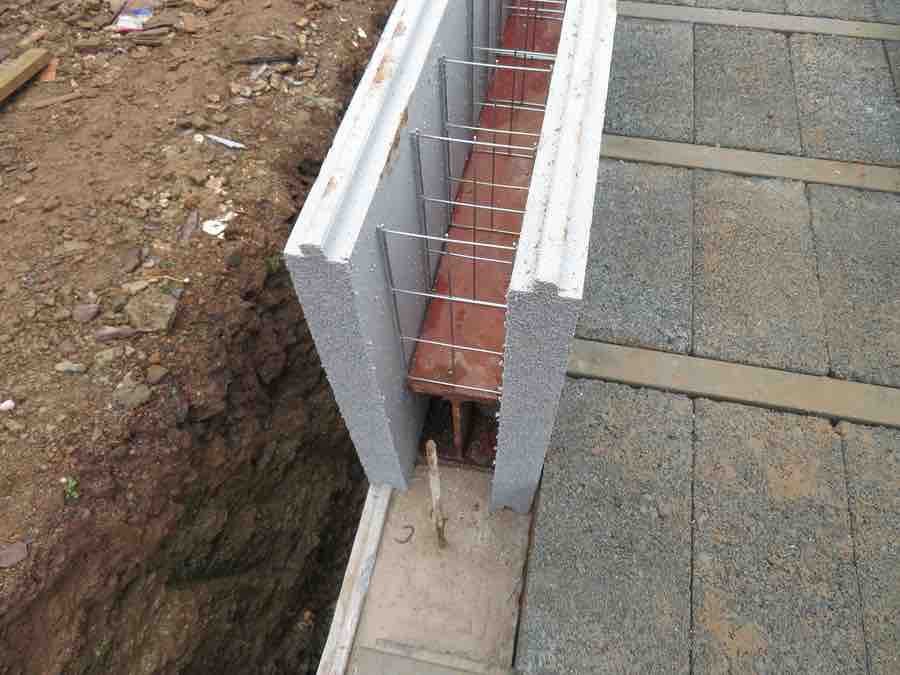 |
This shows how the polybloks can be designed to bridge over voids. The steel beam provides support during concreting and also acts as a lintol. If temporary forms and strutting are used the polybloks can span over quite large voids by the addition of a few horizontal bars over the void, within the polyblok wall. |
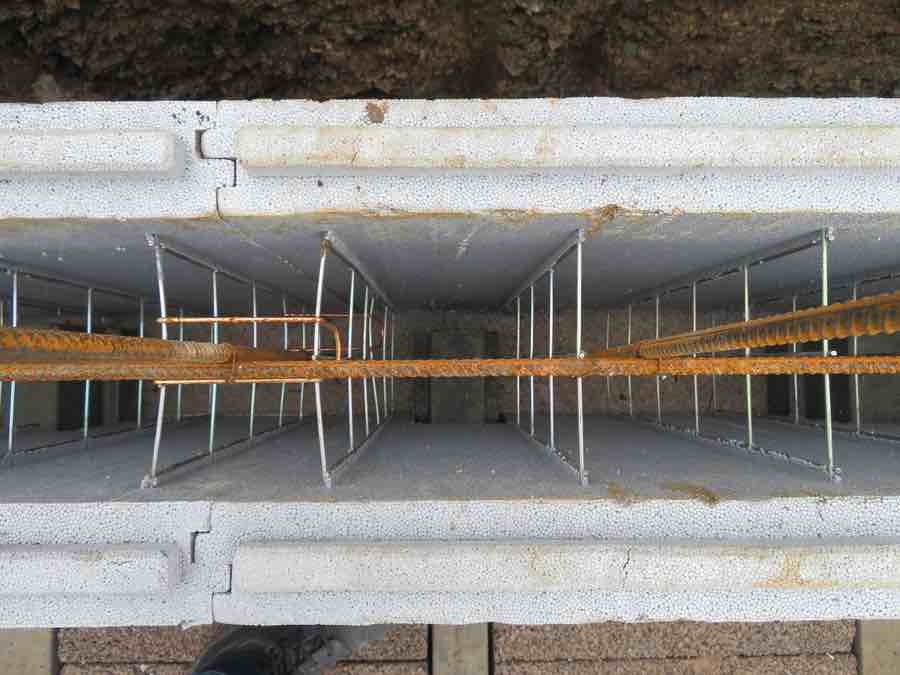 |
This image illustrates how the polybloks are made. The stainless steel wires are connected to 70mm wide stainless steel strips that lie about 10mm inside the outer surface of the polystyrene leaves. They hold the leaves together during concreting and can also be used for fixings using self tapping screws. The vertical rebar is spaced at 300mm c/c to suit the 150mm wire spacing. |
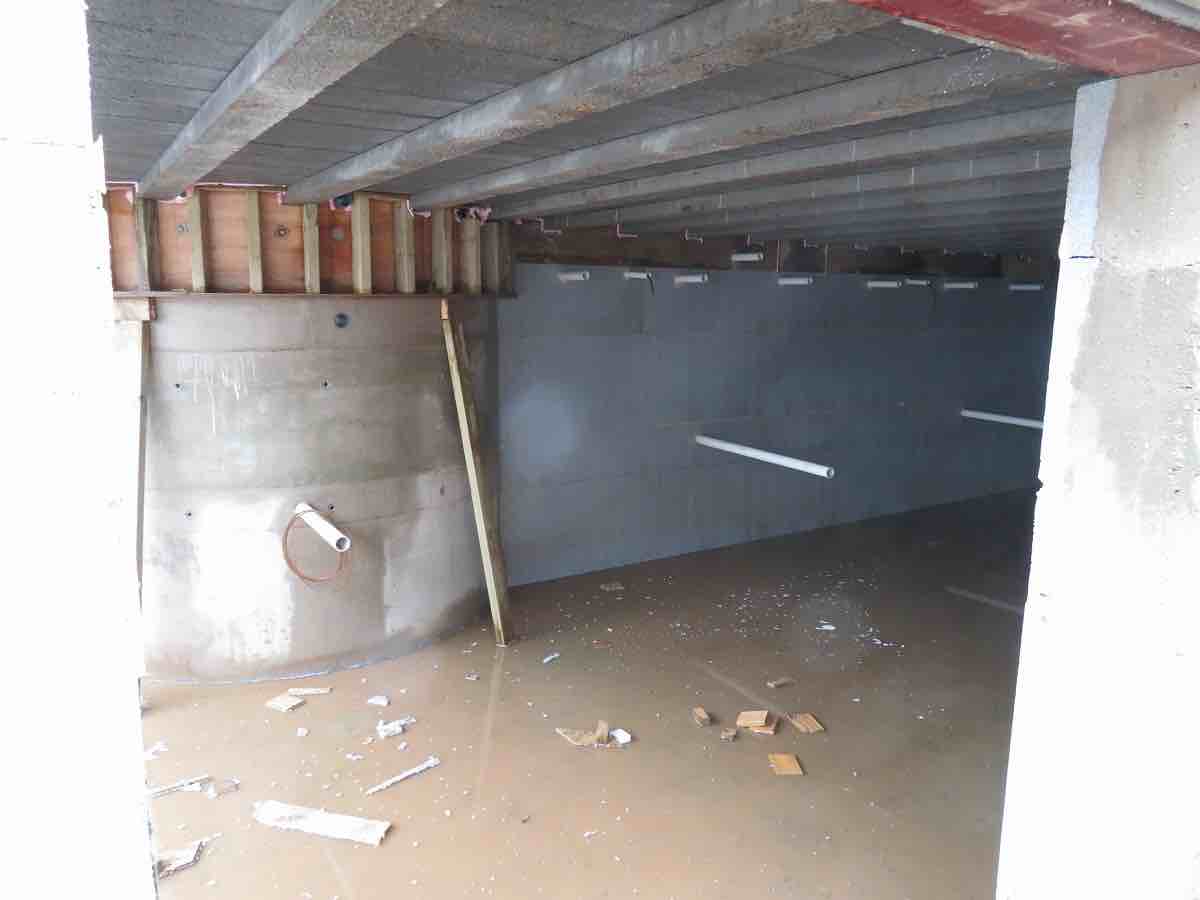 |
The view from under the beam and block floor showing the submerged light and water inlet fittings. |
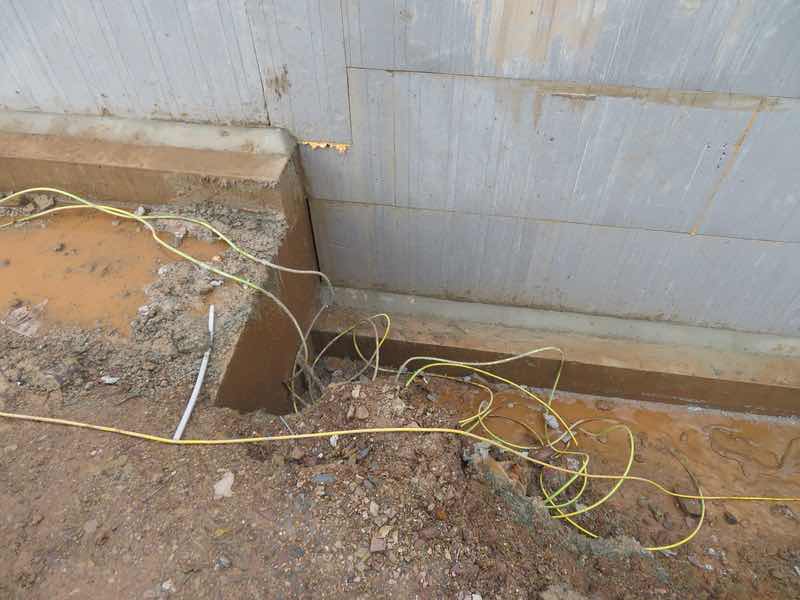 |
This shows how easy it is to form steps in the polyblok walls. |
 |
Many basements require protection from ground water entry. This can be provided by very costly tanking but Bluepools normally installs land drains like the one in the image. This will stop any water collecting outside the basement walls and transfer it to a soakaway in the valley below this pool hall. If the site is level it is sometimes necessary to provide a sump with a submersible pump that dispose of any water accumulations either to a local ditch or sewer. |